G’day Mark, great post well done doing the lam all in one hit! I find when I use a vac lamination and do it with release film like you have done I often get dry spots and air bubbles in the glass, I think air gets pulled out of the balsa and into the glass. So I usually do a wet layup. I use 910 x 100 x 2.5mm balsa sheets I put 20 to 30 gm ones on the bottom and 30 to 45gm ones on the deck I don’t buy any heavier ones than 45gm. I also bag the top and bottom balsa on in one hit, it takes a bit of planing but saves some time.
i would like to know to about the rails mark
i did it that way john on my first board and was really happy with the finish.
tried to glue strips straight onto a board tonight but clamping was a pain…it was a bit messy
definately feel that the outline offcut gluing clamp idea is the easiest
Hi John
The rails were made from 3 x 5mm balsa, cut to shape, then glued with pu glue, taped to eps, then into the bag. I have done them without bagging, and to be honest, the curves on this board are so natural that the balsa curved round nose to tail with no problem, could probably have just taped them on with parcel tape.
I use the 100mm wide sheets, layout my rail templates and plan/cut the scarfs, then glue up on table.
Cut balsa to templates
Glue up and fit to board.
Whole lot takes 1- 11/2 hrs, I cannot think of an easier way at the moment, partic using the gorilla glue.
Hope this helps
I don’t really get the idea of using rail templates to cut your balsa rail strips. I measured my rail templates for a 7’2" minigun yesterday - the hotwire guides? They’re…7’2". But then I laid a string from tip to tail & the outward curve of the rail/template makes the string 7’11". How do you accurately stretch the straight rail template into enough material to fit the perimeter of the board?
Benny
I use my hotwire guides and just add a bit of length to the tail, nothin scientific, just make sure they are long enough. using the hotwire guides is a bit wasteful, as they give a thicker profile than needed, but i would rather err on the generous side.
wouldn’t you just use your rail cutoffs to draw out your pieces and then template from that?
or do like i did…
thumb tack some butcher paper to the side of the straight edged rail line and draw out a new template for the rail bands you adding back on… should be pretty close to final doing that…
you’re gonna use a box cutter or band saw to cut them out anyway so you don’t really need the jigs anymore…
gluing pieces up to build a big balsa sheet seems to be the big short cut…
I guess it’s like cooking… prep prep prep
yeah oneula
i glued up a sheet in the vac bag and it was just like a piece of balsa flexi ply
i did a two ply last time. but next time i will probably do a three ply… just use hotwire guide bottom edge as a ruler to cut full length bands with exacto knife…I really found gluing up say three bands really easy, using the EPS offcut from cutting the outline of the board as a jig … its easier to glue up in a female type jig and u use a lot less tape as clamps…honestly took me about 1 hour to cut and glue bands then glue onto board blank this way…
when i tried to glue them straight on to blank i used a lot of tape and it was messy…im going to only do it with the jig from now on
For the wrinkels, I haven’t tried using release film. But if you use a fine weave peel ply, wet it out just like the laminate and squegee it down nice and tight like the lamination, then put the breather over that, you won’t get any wrinkles.
It usually does take me 2 thin hotcoats to fill all of the texture left by the peel ply but most of that gets sanded off.
Here’s a kiteboard I did a few years ago, viewed from the tail, 9mm thick wood core with 6oz glass top and bottom laminated in one shot. If you look closely you can see the flash seam in the middle of the rail, also a little bit of the glass weave - I should have put on one more thin hotcoat before sanding.
Squegeeing down the peel ply sounds like a good idea. I think that next time I’ll also put on the bottom peel ply as soon as I finish laying the glass then flip the board and glass the other side.
I thought that I would add a couple pictures of a bagged on 11’3" board that was done in a 85 degree garage.
This picture is an adaptation of my folding and Mr. J’s rolling the glass.
I put the rolled up cloth into a wallpaper wetout thing, poured the resin over the glass and let it soak in for a while. I kind of rubbed and pushed the resin into the roll. On the second try I was able to get it to wet out completely. When I unrolled it 3/4s of the way I wet out any wet spots I noticed.
This is the perferated release film. I cut it roughly to shape then took it off the board to put on after I glassed it. I used it in strips with no problems. It was actually easier to work with than 1 long sheet.
This shows the perferated release film, paper towels and the shade cloth. On the bottom of the board I used a full sheet but I found it worked much better with just a strip.
Heres a closeup of what the bumps look like. On this board I only had a wrinkle or two. I’ll see how the deck turns out (its in the bag right now).
Here’s how the laps turn out. I could hardly feel them. I few strings stuck out so I sanded them off.
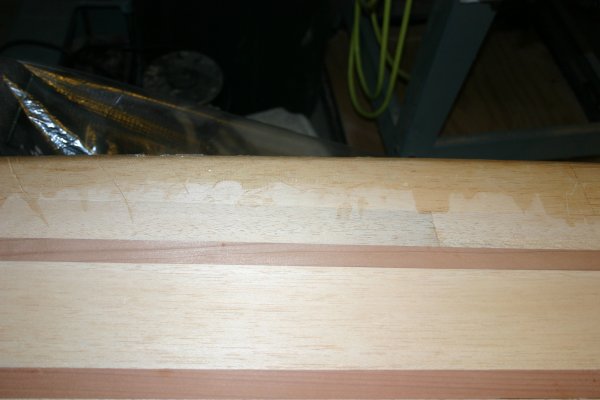
You’re doing a good job Dan.
Maybe I should put this in the swaylopedia, but the stuff in your pics you refer to as peel ply is actually bleeder ply, perforated plastic.
Peel ply is a woven material, and when peeled off leaves a flat, rough surface ready for any further coating or bonding.
I like your idea of the shade cloth to spread the vacuum, good thinking. Does the rough patterned cured surface give any trouble to sand and finish?
I can tell that I typed this too early in the morning. Actually, it is perferated release film (I’ll change it in the post). Last time I sanded out the bumps, but I really don’t think that it was necessary so this time I’m just going to hotcoat it an see how it works. This is the way that Markyv does it and his boards look great!