As an aside; My feelings on war and those that serve are common to yours.
Ha! Made me laugh for the first time in a week. You’re right on Huie. But I’ve always though sanding was where the real money is . Of course if you can fill in doing the other aspects of the process so much the better. I’ve got my own gig and when I get bored I can go down to the Little N------a river and land a couple of whopper Salmon. If I were 40 years younger I would go Down Under and show that punk how it’s done. I love piece work.
"or grennough when did he ever shape in a production manner? for christ sake it was just a bloody fin sooner or latter someone would have used a template much the same
…spot on Huie! Those early days at SB Wilderness I was told, “George would come and go in the shaping room and close or lock the door and we would hear clunking nd thumping noises that you would NEVER hear from anyone else that shapes… we would all try to figure out what the hell he is doing in there!??”
That’s so George!
What Deadshaper hasn’t copped to is his alter ego. The Zappa quotes nailed it. '70’s horn section. At times with Don Van Vliet the Cap’n.
Blow man Blow. HAH!
…yes Huie, always be the same; It s kind of to have the opportunities what I say; if the traders, etc do not let a space for other guys that show the thing, how the designs will change or the perception will change or we can keep this labor alive in the right path?
I was one of the first to emailed Yorky guy and he told me that there s no more place then he put again the thread searching for workers…in my opinion is a joke to see how many people with skills are interested and laugh on us.
**Captain Beefheart anyone? **
More correctly BF aka “Fossil”.
Okay, so now the kitty has gotten out of the bag. In ‘my other life’ I am a famous trombonist playing with Zappa and the Mothers (1973 - “Overnite Sensation”) thru many other albumns incl. 1978’s “Studio Tan”, 1988’s"Broadway the Hard Way" and more all the way thru the more well known “Cheap Thrills” (1998). Other projects include “Breakfast for Dinosaurs”, “Last Blue Sky” & “Eyebrow Razor”.
I guess this thread has ended up with more drama than anyone needs for the New Year, with wrongs being righted, Reverb pondering his very existence, shout outs to vets and soldiers and all the rest that makes for a twisty turning Swaylocks thread… FGH…betcha didn’t know what you were getting into!
(-:
and then there is this
enough i say
Selling on eBay, http://m.ebay.com.au/itm?itemId=261380538981
Hey Bruce-------- Just came back from Loews. Lots of various density foam trowels in the plaster/mason tool section. Far wall. Front of the store. I bought another wooden trowel from Black Hawk. the wood is dense,hard, flat with turned edges. Makes a great sanding block. Going to glue Walmart EVA on this one.
Thanks for the update… where the hell is the nearest Loew’s? I saw one down in Ven-Tuna, but I’m up in Solvang (Danish for Sunny Field). I’d rather go north versus south any old time.
Not to hijack the Ryan thread completely here… I think it is cool that RL can travel and shape how he has been doing it. That’s not an easy act to put together. I have a guy that just p/u a Stoker V Machine for the U.K. and wants me to come over and shape quite possibly in the same factory as Malcolm Campbell does, and some others have. These guys want the glass work, and after tossing it back and forth on how I could do this, most recently I had to write back and say that i don’t really have the time to do a traveling gig with the work I am doing here. I suggested sending shaped, signed blanks to probably Portugal and they would “Chunnel it” with a van and go pick them up.
The ‘have planer will shape’ travel gig is romantic and all, I just don’t have the time after setting up my production with Hawk, having a solid crew I know and trust… blah blah. I’m already in an “East Coast summer state of mind” starting to build “Production Customs in 3 inch increments” from 5’3" to 8’0" in both Stoker V Machines & my MiniMAX… that’s a lot of boards to have on hand (and constantly restock) for a new program I’m calling “Quik Ship”. If I don’t do this now, once we get near summer, the whole goddamn Eastern Seaboard wakes up and everyone hits the Jersey Shore to be a surfer again.
Add to that, shop’s like Mollusk (Venice & SF) and Saturdays (NYC, Japan), Z aks in OZ, my Japanese distributor, Wave Front, Surfy Surfy, and… well, you get the picture.
Ryan handshapes one at a time in “an hour and a half”… he has said by the time he would drive to "I Shapes down in Ven-Tuna bring them back to his shaping room, gets to work, that he already could have shaped a couple of boards. So his method works for him.
I have one off handshapes piling up right now, and they are gonna take the time they demand… no compromises ever on those… Some are “magic boards” guys want a fresh one and one is a scaled down EPS/epoxy by 6" but still the same shape.
Now Matt Wessen tells me last week he and former French Champion, Gege Brasset (Tom Curran’s nephew) want two 8’6" to 9’6" Stoker V12’s to ride "20 to 30 ft. faces at Guethary. That kinda stuff takes TIME!
I still love hand shaping, but if I did my whole business the way RL does it, someone would have already ordered a hit on me.
Such a rad ebay find! haha!
double
Reverb says:
…hand shaping is the prove that you can shape clean lines…in the other hand, machined is the way to prove that you cannot really shape clean lines (and that the person is not a craftman or a candidate more like a businessman) , and that s a fact more if some one think that can hand shape, included templating, pre shaping (trueing, etc) finishing custom orders in no time.
Yes, and… no.
Let’s talk about this. I think Huie could attest to the fact that the CNC milling has become the norm for many shapers trying to make a living in the industry while offering a consistent quality product in higher numbers that enables that craftsman to supply demand at a competitive price.
The proliferation of Models exacerbates this position as some companies carry so many different models (C.I., Lost, Proctor, DHD, MC, McTavish,Bing, Cooperfish, Firewire, Rusty, etc.) that one guy doing one offs could never begin to approach shifting gears fast enough to be a player in that arena.
…I’m not suggesting that you even TRY to compete on that plane, because it is a different business model altogether. Now b4 you go getting pissy over the mere mention of the word “business”… there are plenty of guys that are in business that have souls that are dedicated to producing good quality products to their customers. Your approach is very pure and individualistic, but also very limited in what you can realisitically produce.
This will appeal to some consumers, but not all.
Your assumption that shapers using files and cnc machines lack the talent that a handshaper has is true for some, but certainly not for all. That’s actually naiive if not downright ridiculous.
**Huie showed me a fin that he did on his cnc a couple years ago… it was absolutely primo. Guys like Laird Hamilton are doing programs for SUP handles with Surfding (remember him?) on his software for machining. The capability has gotten so advanced your original lines that took a lot of blood, sweat, and tears, can now be faithfully duplicated to 95% of completion. **
The ability to scale has improved dramatically, as well as the ease of creating subtle modifications from the original file to try something new without having to handshape a whole new board then having to scan it.
However, unless you are one of those experienced and capable designers, that is more than likely backed by years of disciplined handshaping, I completely agree with you that those computer shapers that think they NEVER HAD TO LEARN TO HANDSHAPE because the computer will fill in all the blanks and just do it for you are in for a rude awakening.
Sure, some of them will ‘get lucky’ once in awhile… it was the same for guys that handshaped and NEVER used a rocker stick. I know guys like that from ‘our era’, and they were always hit or miss… the younger generation of ‘straight to computer’ shapers will also be hit or miss… albeit ‘their miss’ will be with more precision.
“Welcome to the Machine”: You can love it or loath it… or anywhere in between, but at hitting 62 this Christmas, the reality for me was how to practice preservation so I could productively continue my lifelong passion. Yes I still handshape, but I also have incorporated using files and techniques that save from a wearing out a rotator cuff, a wrist joint or having lower back problems much like professional tennis players, baseball pitchers or golfers that have repetitive swings in their respective motions. Do you think Brewer, Hynson, Rusty, Stretch, Haut, Arakawa, Aipa, and many other older shapers still handshape everything start to finish? Guess again.
I have long maintained that there are guys that will shape masterpieces that will put my every day work to shame. I’m also aware that some of those $5000 to $8,000 wood marvels that some legends claimed to have handshaped, were actually machined because I know the guy that quietly machined them.
I’m happy making an affordable ‘utility model’ that lots of people have fun on if not embrace. I consider myself very fortunate, but not really “lucky” as I’ve worked hard and smart for years to be in the position I’m in. The deciding factor has very little, if nothing to do with being in California as you seem to attribute a large portion of success to non plus boardbuilders you saw in Japan. I’m sure your discerning eye caught a LOT of crap.
My understanding is that you are in Australia. If I’m wrong please correct me. I know you make a super quality product. There are hundreds of thousands if not millions of surfers in OZ. I would think someone of your talent could sit down, crunch some numbers and figure out what net profit you are happy with formaking X amount of boards each week while attracting and retaining satisfied customers. After all, you ARE in business, any way you slice it, and at the end of the day, you have expenses and gross income. It’s not rocket science. If you wanna make $1,000 bucks a week shape 10 boards where you net $100 each, if you can’t shape or get that many orders do 5 to net $200 per board. If you are doing the boards start to finish, figure you should make what the glasser, sander, painter, glosser, fin guy, polsher would all make piecework, along with the shaper and you might be able to make even less boards per week to hit your target weekly income. Everyone is different… some guys might be shaping 20 per week at $50 a board…or the CNC scrubber guys do 2 per hour at $17.50 per board. Those guys can do that all day long and are happy to make $35 an hour instead of working some other job getting barked at by a manager or given “busy work” that makes no sense…
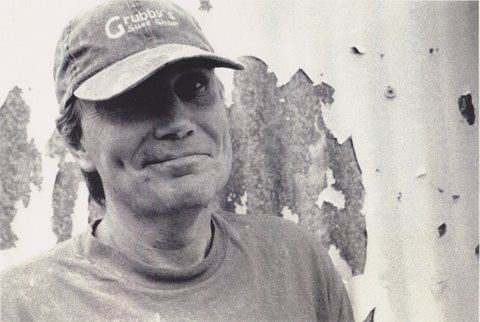
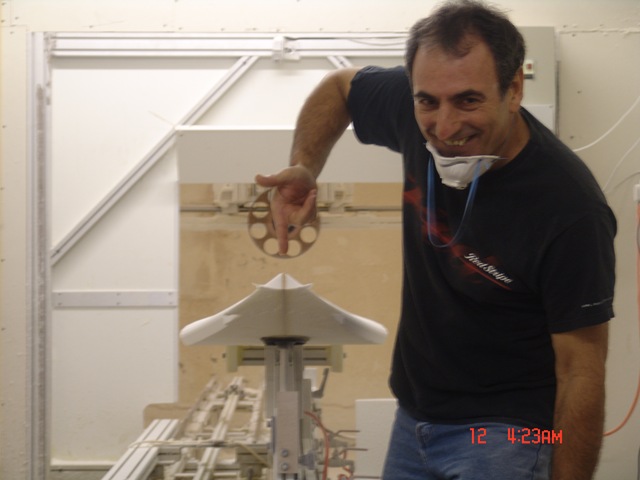
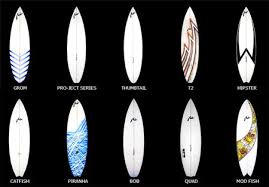
…hey DS, may be I explained it in a not so good way; I tried to say something along what you wrote; that with handshaping (more if you do all) you can SEE that the guy may or may not can or cannot shape and got fluid clean lines out of a custom order not following the lines of a close tolerance…
-I m very tired of the miths, pseudo masters and that “yeah; I shaped n thousands of boards” thingy; due to the real fact is like very well Huie mentioned, other.
I am not proclaim anything about my boards, nor that Im a master; that Im not; but I work hard on it. I try in the other forum to help with real tips and from time to time I post some photos of my work; nothing more. I believe in build all the board and know exactly what s going on and become very good at all the steps; steps that most shapers do not how to deal; even great % of old timers and masters.
-The real numbers are like these: if some build all the boards by himself included making fin panels, foiling; doing custom orders with complicated airbrushes, color work, special fins, intrincated shapes and fine quality, a competent builder can do no more than 120 boards per year; same but without fins, clear sanded boards without intrincated things you can top to 250 per year, working all day.
I charge a good profit for the boards.
Not bad at all, but lot of work and that s what I m pissed off; not the money; hearing and seeing that opportunities are not for every one.
I checked poor designs and so so craftmanship but with top quality glass work that hide all things from the inexperienced eyes.
Also I saw machined longboards that have a fine design (yes, I mean design not the work of the shaper) and fine glass work, 10 DAN glass work. Fine product and board possibly.
I appreciate your clarification on stuff.
I know where you are at… when I had the Underground in the Radon Boatyard, we did ALL our own stuff too… fin panel layups and full production of ALL our fins regardless of what they were. We cut and glued up special blanks both in poly and EPS. I could do everything start to finish and would do what I call “sketches” which were one day boards that I would go ride at the end of the day… this was long before UV resin.
You are VERY right about the guys that can shape and know how to create clean lines without twisted rails. Guys that don’t know their rockers are twisted and if they are looking at a dip or a bump or a flat on the rail… nor how to even approach getting the problem area corrected.
Truly good shapers are DISCIPLINED people. That doesn’t have to mean they are disciplined in every day life… though that may frequently be the case, but I have known guys that were disasters in their every day dealings and keeping things together, that, once they got into their shaping room, it was like some miracle switch they could throw and create beautiful equipment.
My friend that does files down south told me "so and so name shaper told him “your work doing a file on my boards make me better than I am”. That is an honest statement that I applaud that old Island surfer shaper for being able to even say.
So True!!!
Looking at the “Surf Hipster Starter Pack” I’ve decided the name is wrong.
If I bought it off ebay, I’d be more than satisfied to pack up ‘the pack’ and RETIRE with it to some tropical surf destination never to be seen or heard from again.
The boards would work well in every type of wave I’d ride for the rest of my days, and all the other stuff would be perfect for passing the time between surfs, fishing, and climbing coconut trees…
…always wanted to learn the ukelele.
I’m hearing you! Wash up on deserted island (that had electricity), watch morning of the earth, wear tight shorts, read 60’s and 70’s mags, channel your inner midget style, play uke, listen to jazz, trim the beard, talk to Wilson.
You would have the island to yourself, passing sailors would be scared to approach!!