If you had a 30’ x 50’ (17’ tall at one end and 15’ tall at other) space and where a one man show how would you set it up. Full blown factory. Shaping and glassing.
What a gr8 space to st up your dream shop! I’ll offer you up some past experiences of mine with shops I have had of varying sizes without getting overly specific with too many imds… more along the lines of what worked for me and my crew back in the days of full production. Also, I don’t know where you are located and what permits and limitations you have by agencies imposing things upon you. Here goes:
When I built The Surfing Underground in 1981, it was after returning from Santa Cruz while managing O’neill’s Surf Shop. Once back in my hometown of Santa Barbara, it didn’t take long for people to start contacting me for new boards although I originally reurned home and begin tending abalone for a couple of divers then diving myself when the sea urchin thing took off. Back in those days, all I had to have was a tender’s license to be able to dive urchiins. Each day I’d bump into guys at the SB Harbor and more and more orders would ge requested.
I went over to the Radon Boat Yard at the bottom of Santa Barbara Street, a block off the beach and the same spot I had worked building Radon boats with the Radon boys, Mike, Donny & Ronny under their father as their design was alll the rage for commercial diving in the Channel Islands. I had had a shaping room there in 1972 when I revived the Owl Surfboards label for Surf 'n Wear which eventually I would partner with Jeff White adding a Goleta, San Luis Obispo, and Thousand Oaks store. At that point, I handed off the reins of making the Owl’s to Marc Andreini, as my work load of being General Manager was a lot of responsibility and I was stretched thin. So in short SnW years spanned the 70’s, then a 80-81 stint at O’neill’s then back to SB.
In late 81 or early 82 I was back over to the Radon Boat Yard where “Uncle George” radon had taken over managing the boat yard. There wasn’t any active boat building like there had been in previous years, but there were a lot of boats stored and lots of spot repairs, some metal fabication going on and some other shops doing upholstery and other types of businesses in the yard at that time.
My old shaping room was still there tucked back behiind one of the roofed but open boat bays alognside a little creek that was more of a drainage ditch that ran down to the beach. Someone had used it for a storage and it was now available so I snagged the 10’x20’ room and asked about the roofed bay adjacent to it. George said I could rent it for a pittance.
We got along really well and I told him I’d like to put a floor in the bay and frame it out and make a real shop out of it to do some glassing & repairs. Not only was he amenable to the idea, he told me he had worked in the concrete business for years and he would show me how to build the forms for pouring the foundation in the new space. He told me the cement trucks frequently have extra cement not used in a day’s work and look for a place to pour it off, that I could get cement for FREE!
Long story short, this all happened according to plan, and before winter set in, I had a new repair shop/glassing room of around 450 sq. ft. with 4 down racks with ample room to move between them. At one end I set up a “squirrel cage” fan that pulled the fumes out of the building, exhausting toward the ditch behind the shop. At the other end I framed and hung a couple rows of pipe that allowed us to have rolls of fiberglass that would slide over in front of each respective board on a rack allowiing us to pull the cloth out to it and trim the glass previous to laminiating it. I’d liked this method as it kept us from moving boards around less as if we had only one rack where the boards could be “dressed” before laminating.
For the time being, the shaping room doubled as the sanding room, less than a perfect scenario, but before long, I was able to jump next door and take the space some other people had occupied which allowed me to build two 10’x20’ shaping rooms with high celings. Next to that was a large spray booth for airbrushing and other spray work we were doing. The spray room was tricked out with sparkless switches for the fan because, by that time, I had started doing a lot of sailboards and we were spraying some pretty noxious and technical finishes like Linear Polyurethane and Emeron.
I really liked havinig big, generous, shaping rooms like that! I had decided to do the rooms this size because Bob Krause (rip) and I had gotten heavily into windsurfing and we had guys asking for “Pan Am’s” which were 13’2" at the time. We were doing hundreds of sailboards per year along with surfboards, and we had become the go to shop in the area for repairs.
With our success in the sailboard market we kept on adding people and growing, it wasn’t long before I jumped next door to the shaping/painting building and rented another already enclosed boat bay. This one had a room in the very back that connected back to back with my original shaping room (now sanding room) from 1972. I made that room a dedicated polishing room.
I connected the whole place with doors and everyhing sort of worked clockwise from one stage to the next to provide a smooth flow from shaping to painting to glassing, then over to sanding, glossing then off to polishing. We also had a smaller area for our own fin production lauyp, foiling and an area we were cutting & gluing up some of our own blanks. Throu the 80’s, the place went from 450 to about 4,500 sq. ft. all said and done and I had a crew of about 8 guys all working together.
Depending on how much production you’re going to do, 1500 sq ft. is a fantastic size for one guy to have to play with. Like I said, generous sized shaping rooms really worked for me when I look back. When I shaped for Clyde Beatty before his move to China, we had a large quonset hut a block down the street from the glassing factory which had historical been the Yater shop. In the quonset, we had Steve Brom, Wayne Rich, myself, Max McDonald, Lauren & Renny, and Kevin McClelland, all with our own respective rooms built to personal preference. My room was 10’x20 or 25, which gave me lots of space to template boards, then stand them up for viewing, etc… High ceilings are a huge plus in a space for surfboard production, blank storage, etc… .
Since you’re only one guy, the need for a lot of ‘down racks’ in a glassing room may not seem very important - the thinking is you can only glass one at a time. But if you are really keen to make a living from such an operation, you should be able to hot coat or gloss at least several boards on racks at a time. It just makes sense. If you are doing production, you want a LOT of wall racks that have carefully been built that don’t have boards twisting once they are glassed and placed along the wall spaces you have.
Aother word on shaping and sanding bays - POCKET DOORS RULE because you don’t want doors swinging open at the wrong time should you end up having people work with you in the future. Maybe you will be successful and grow your business, and it will have been insightful to build sliding pocket doors from the get go. They save space, and aren’t that hard to do.
You probably would be well served to have the sanding room and shaping room adjacent to each other. They are the “dirty rooms” although if you set up a vac system for your shaping room this will keep the sanding room as the main area that begs for good ventilation that can pull air thru it. We had a huge fan that went thru a deflector of sorts that exhausted toward the creek/ditch and it sucked so much air thru the sanding bay we had to cut “feed slots” at the opposite end of the room with deflectors that directed the air being sucked thru the place directly over the board being sanded, which was freestanding in the middle of the room versus being along a wall. Like I said before, it had been a shaping room. Yater’s sanding room was different from mine. With his, you would but the board along a wall and there was a fairly skinny slot cut into the wall that his system sucked the dust into it and it went up and out over the roof of the factory.
Yater’s factory was designed as a surfboard factory from the very time it was built. I never knew that until Sonny Castagnola told me that he and his brothers, successful fisherman that came to Santa Barbara from Italy, and bought up tracts of land near the harbor, approached Renny and told him “if you design a factory for yourself on our land, we will build it for you”. True story. Clyde Beatty took it over when Renny wanted to slow down, because it was grandfathered into the area and permitting was already in place. Eventually Beatty left for China and the new era unfolded.
Anyway, I hope there’s a few gems in there to help you with you new space from someone who still has fond memories of my building past. It’s a lot of fun to think about your space and what worked for me as I grew my business back in the 70’s & 80’s. Over the past 8 years or so, I got back into doing boards from start to finish on my property at home then got burned out due to the volume growing and handed it off to Haakenson at his 5,000 sw. ft. factory iin Go Go Goleta. I shape at home then run them in to see the crew including Efrain, who was a young man from Mexico that came to me at The Underground looking for work way back then. I taight him how to glass and Hawk says he’s one of the best glassers he has ever had.
Have fun and be proud of what you make!
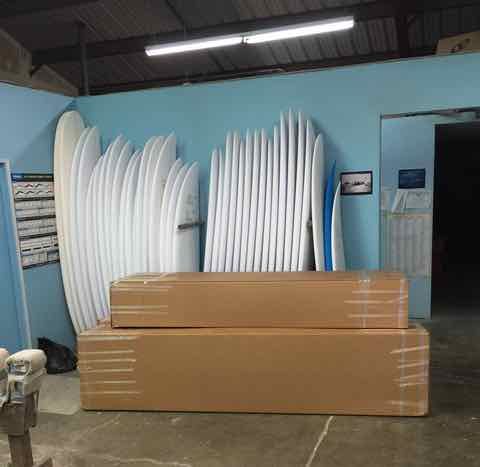
16’x12’ bay with full vac system and a huge exhaust fan on one end. Run piping not only for you dc but for your compressed air so one unit can power the whole shop without long hoses. then a small room to put the dust vac unit in then you have a massive area for glassing. I would have a stand with all your cloth on rollers so that way you can just roll your cloth to each glassing stand. Set up as many stands as possible without crowding (depends on how big the boards you make are) if it ever gets cold and you like using uv consider a rack or stands with a few uv fixures around it. a few air tight containers to keep your resin supplies and your all set. depending on your heating/cooling you might want to hang drop ceilings in the glassing room to keep total air volume down. I am super jealous.
Some awesome stories you have there. Thank you for sharing!
(3) 10’ wide bays in the back. shaping, sanding, spraying. fan in the sanding and spraying bays no doors needed.
carve out a chill out / board display area in the front. next to that setup an area with garage door for foam storage / hotwire setup
all the space in the middle for glassing. might want to build a small enclosed area along one wall for glossing or heating up for epoxy or wintertime glassing.
setup a vacuum bagging area along one wall
something that might be nice i dont know where you put it is a place to woodwork - bandsaw, planer, etc
with space that tall, you could have a mezzanine
another thing to think about with a space that big is you could set up a CNC for boards
thinking about it, a mini CNC would be awesome for fins
Bruce, excuse me if this is a dumb question, but that dust mask won’t protect you from resin fumes will it? Mike