MATERIALS USED: from Fiberglass Supply
I wanted to add a list of everything I ordered from www.fiberglasssupply.com including prices and product codes in order to make my board. The amount/number of each item reflects what is needed to make one board. The 1.5 gallon kit is around $100 and can make roughly three boards if you do not waste and work efficiently. So, if you plan on making more than one, it might be better to get the 1.5 gallon kit. Otherwise, stick with the 3 quart kit if you are doing one board. Here are the items orderd for my board:
Resin Research Epoxy Kit 2000 w/ 2100 Fast Hardener
Amount: 3 quarts
Item Code: G02-0130
Price: $52.48
E-Cloth Fiberglass Fabric (6oz X 30")
Amount: 12 yards
Item Code: C06-1308
Price: $45.12 ($3.76 per yard)
Additive F (sold in pint/quart/gallon)
Amount: Pint
Item Code: G02-0250
Price: $15.75
Sailboard 5/8" Retrofit Vent w/ Thumbscrew or Slot Screw (your choice)
Amount: One
Item Code: R62-5120
Price: $1.77
Grand Total: $115.12 + shipping
**These were the only items I ordered from Fiberglass Supply. Everything else can be obtained from your local Home Depot, Hardware Store, and Craft Store.
EDIT: 8/4/06
So we worked on the top today. Attempted to do a tint inlay. Decided to go wtih a light blue, mainly so I could see how it turns out for future projects.
First, we taped off the rails. Do a good job on this so there are no leaks. Also make sure you leave enought tape hanging down off the rails so that if it drips over the side, it won’t get on the bottom of the board. Learned that the hard way. We covered the board in one layer of glass and cut it to the length of the board. No trimming this time.
Mixed the tint into the resin and pretty much did the same to the top as we did on the bottom.
As you can see, the resin dripped down the side and got on the rails just a little bit. Make sure to have tape hanging off far enough to prevent the resin drips from getting on the bottom of the board.
Next up, we cut the lap lines. Pretty much the same as the bottom. Very Carefully.
Its starting to shape up nicely!
Hunter is amazed at his abilities…
EDIT: 8/7/06
Tonight we put the final two layers of glass on the top of the board. Since I waited more than 24 hours to do the next top layer, I had to sand the deck and rails to “scuff” up the board which helps with the bonding process. Apparently when you let the board sit for over 24 hours after the first layer of glass, the chemical bond is no longer prominent and you have to go with a mechanical bond. (correct me on this b/c I don’t think I am accurate with this process) I scuffed the board up real good using 60 Grit Sandpaper, and cleaned it off with "Denatured Alcohol.” This will setup the board for a better bond and a clean look.

Had I not waited 24 hours, I would have just scuffed up the rails and sanded the line where the bottom and top laps meet (green meets blue). However, by waiting, I had to scuff the rails and the whole top of the deck, as well as clean it off with the denatured alcohol to set it up for a better bond.
After the board was prepped, we moved to the glass. The 1st layer was trimmed to match the shape of the board, leaving enough fabric to reach the bottom of the rails. The 2nd layer of glass was trimmed about “a thumbs length” hanging down from the rails. (see pictures) We wanted some big honker laps to make this thing tough.


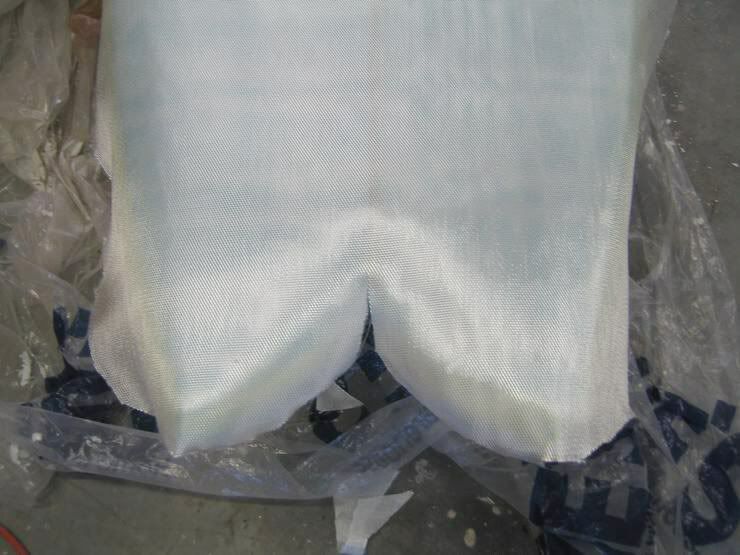
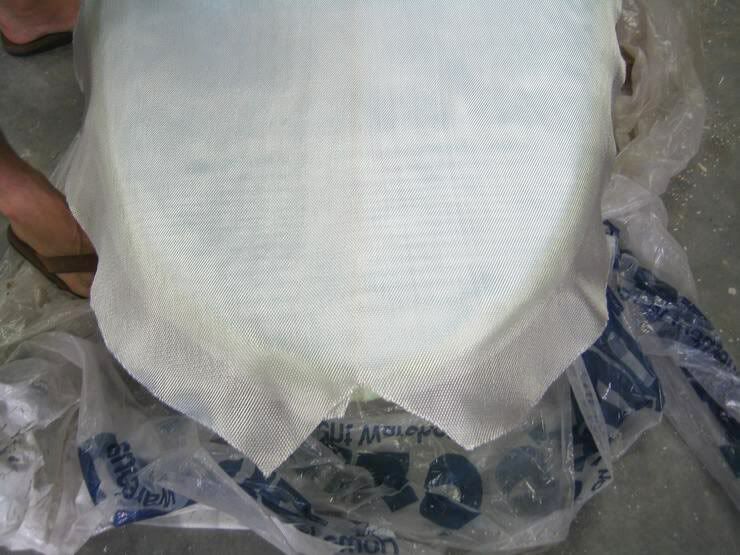
Mixed up a batch of resin using 16oz of Resin, 8 oz of Hardener, and roughly 8 cc’s of Additive F. Once they are all in the mixing bucket, take note of the time and begin mixing for 2 minutes. Stir it semi-fast to make sure everything is thoroughly mixed. However, if you mix it too fast, air bubbles will become trapped in the resin and you will get a milky color to it. Just a good thorough mixing.
Here is a pic of the 3 times before mixing (16oz, 8oz, 8cc’s)
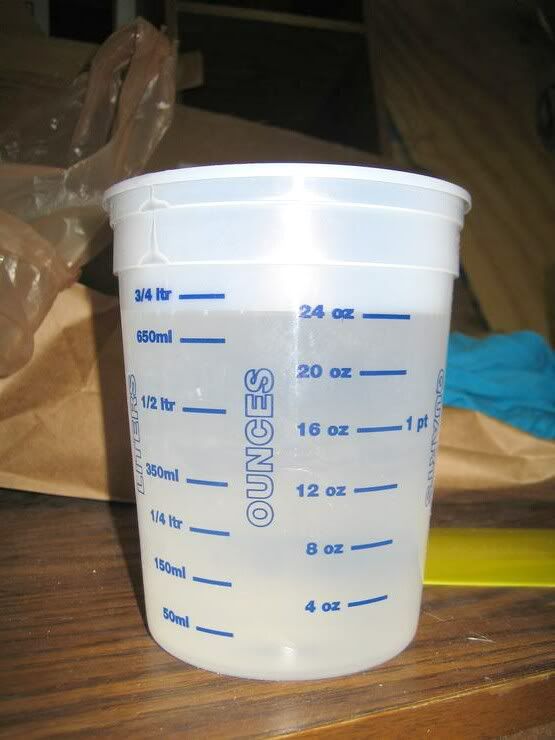
We covered the two layers really good, starting from the middle and working our way out with the squeeges.
After the middle of the board was good and saturated, we began to move the resin towards the rails, soaking the overhanging laps (**Note: I was unable to take pics of this process as my hands were full so the pics go straight to the 2nd coat of resin).
We folded the laps under starting from the middle of the board and moving towards the nose and tail. Here are two pics showing the size of the laps we used.


Keep the fabric good and tight. Scrape the resin from the stringer towards the rails. This way it keeps the glass good and tight.
After saturating the glass cloth and making sure there were no lumps, we let the board sit for about 45 minutes until it became tacky. Took a break to go eat. Came back and mixed up what would be considered the “hot coat” even though there is no extra hardener used….basically just another layer of resin mixed the same way, but painted on with a brush rather than squeegees. Here are pictures of the 2nd coat of resin going on after the first layer had become tacky. Note: the resin has a “milky” color due to being mixed a little to fast. Note to self: do not mix the batch too fast or air bubbles will become trapped and give the resin a cloudy look. We were too excited to get this thing done and got a little carried away on mixing. 


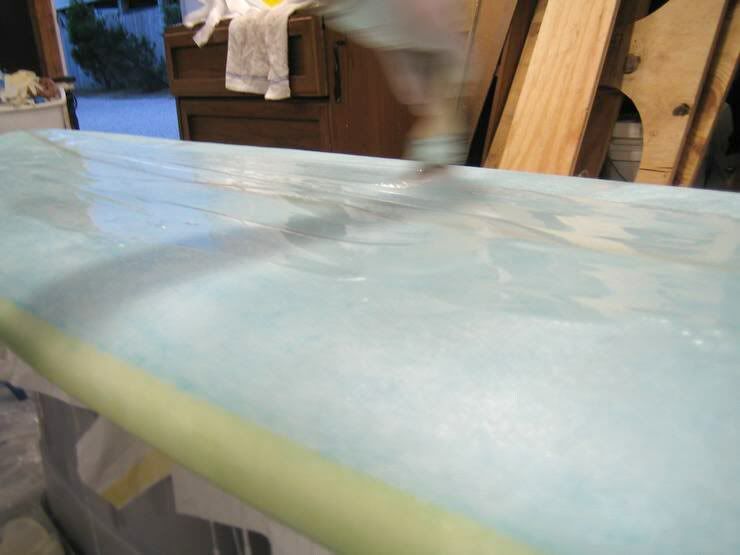
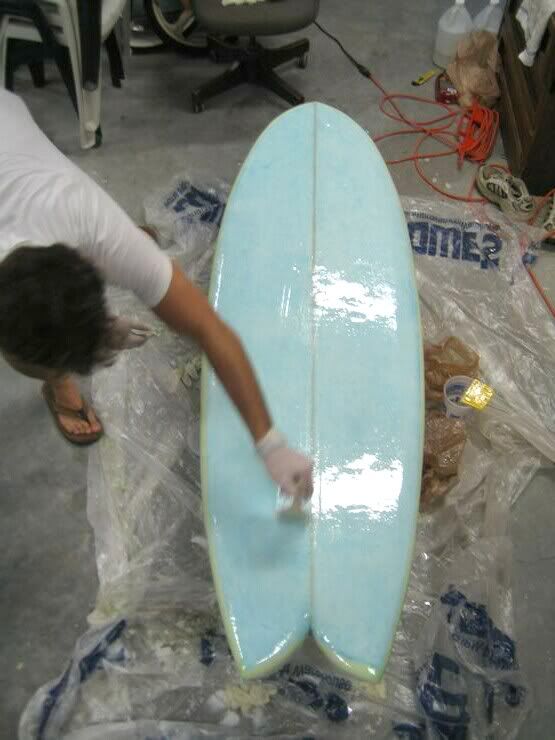

Its finally starting to look like a board. Not too much longer…
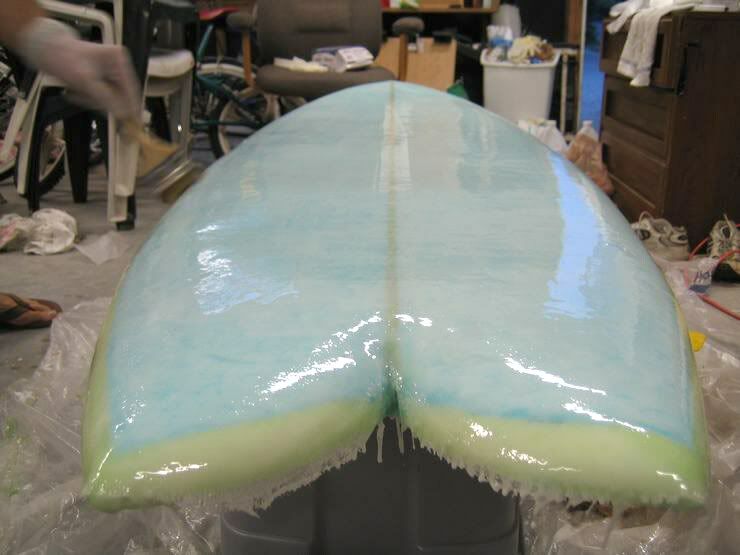
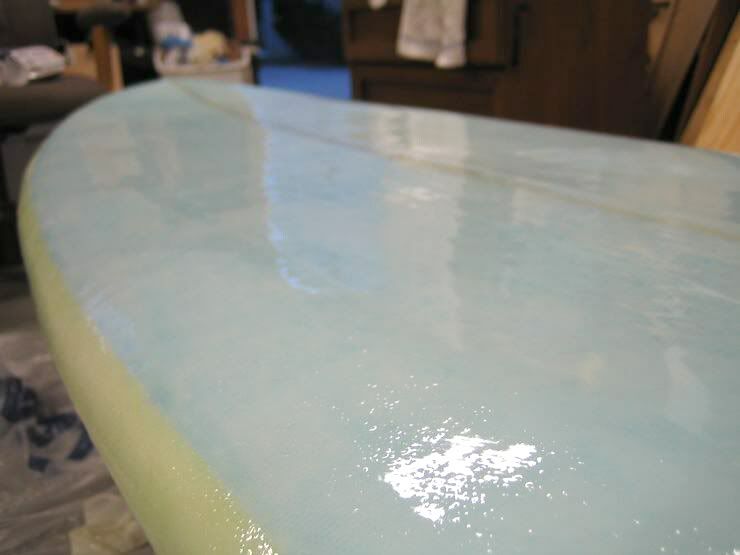

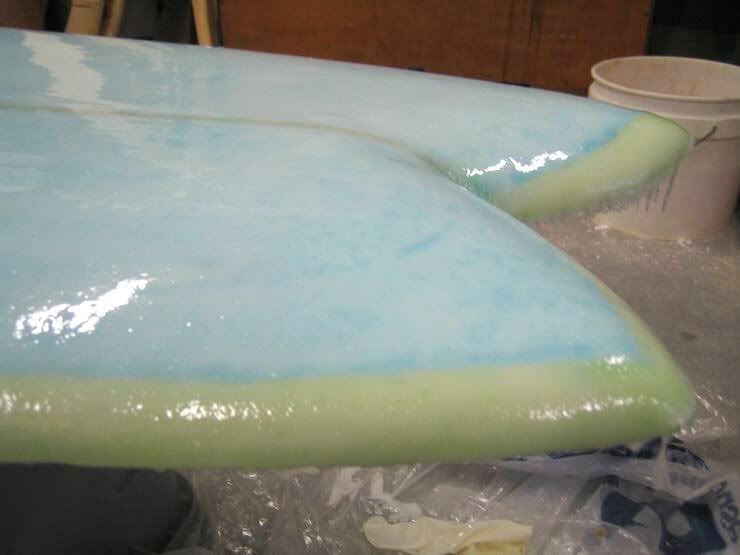


Next up…fins!!! Went up to the craft store and bout a 12" X 12" piece of 3/8" thick plywood - $4.99usd. This will be the start of the fins.
