I messed around yesterday at lunch and made a semi functional plug for making wax molds,
here are some pics of how it was constructed…

I ripped strips the desired widths… the squares that form the wax shapes were cut from a strip also ,I used a slide miter saw to cut the 45 deg, slot before I cut them to length.
I used plywood because that’s what we had on hand, MDF is the best material for this project (and it’s cheaper too).

I didn’t take the time to radious the edges but all corners should have at least a slight radius to keep the plastic sheet from tearing
stapled mdf strips to the bottom board making sure that the joint is tight.


placed the top plate on and arranged the squares (sort of) on the top and fastened in place.

drilled some holes in the corners to allow communication between the top and the inside chamber…

these holes are too big… a lot of smaller holes are better…
then I made a frame to hold the plastic sheet down…
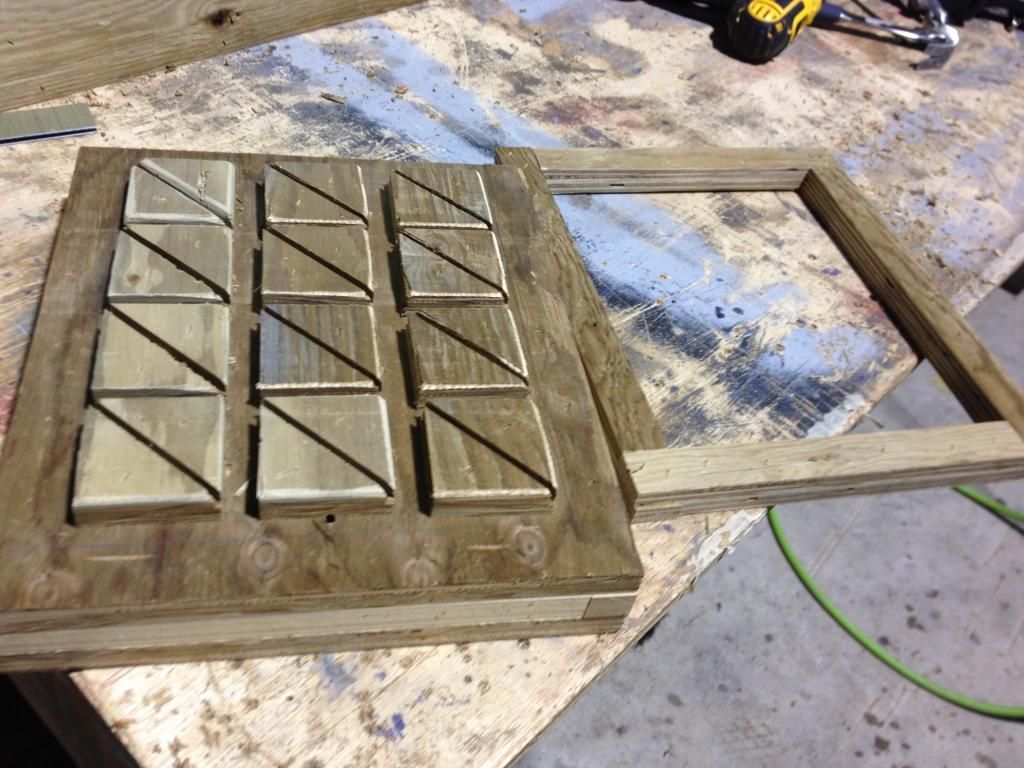
Then I drilled a hole in the bottom plate for the vaccum (no picture required).
That’s as far as I got…but the mold is essentially ready to go…
The plastic can be heated in an oven on a sheet pan to keep it flat…
I’m not sure of the temperature (the type of plastic and thickness makes a difference) it would be best to start lower (maybe 200 deg f )and keep an eye on it…
after the plastic is soft, place it on the mold with the vaccum already on place the fame on top and it should suck down pretty quickly and you might not need to clamp it in place…
If the plastic cools before it forms the correct shape a heat gun could be used to do some spot forming where needed…
That link that hans provided got me thinking about alternative sources of plastic for molding, and one that might work for this would be cutting sections out of the sides of a five gallon bucket,
but also plastic from a cheap picture frame would do… probably many others too…
releasing the wax from the molds is important so it would be helpful to use a plastic that is a little flexible but maintains its shape over many cycles,
lexan would be a good choice (if you don’t have to pay for it)…